The Scientific Research Behind Porosity: A Comprehensive Guide for Welders and Fabricators
Comprehending the complex systems behind porosity in welding is critical for welders and makers making every effort for remarkable workmanship. As metalworkers look into the midsts of this sensation, they reveal a world regulated by different factors that affect the development of these small spaces within welds. From the composition of the base products to the details of the welding procedure itself, a wide variety of variables conspire to either worsen or ease the existence of porosity. In this extensive overview, we will certainly untangle the science behind porosity, exploring its results on weld top quality and introduction advanced techniques for its control. Join us on this trip with the microcosm of welding flaws, where precision fulfills understanding in the quest of remarkable welds.
Recognizing Porosity in Welding
FIRST SENTENCE:
Evaluation of porosity in welding discloses important understandings into the stability and top quality of the weld joint. Porosity, identified by the visibility of cavities or spaces within the weld metal, is an usual problem in welding processes. These voids, if not effectively addressed, can compromise the structural integrity and mechanical residential properties of the weld, leading to prospective failings in the ended up item.
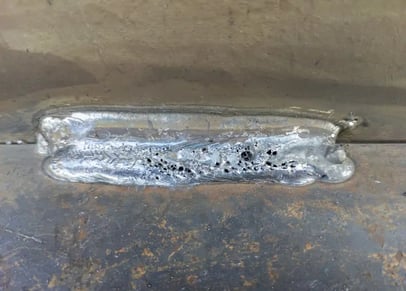
To discover and measure porosity, non-destructive screening approaches such as ultrasonic screening or X-ray inspection are often employed. These strategies permit the recognition of internal defects without compromising the stability of the weld. By analyzing the dimension, form, and distribution of porosity within a weld, welders can make informed choices to enhance their welding procedures and attain sounder weld joints.
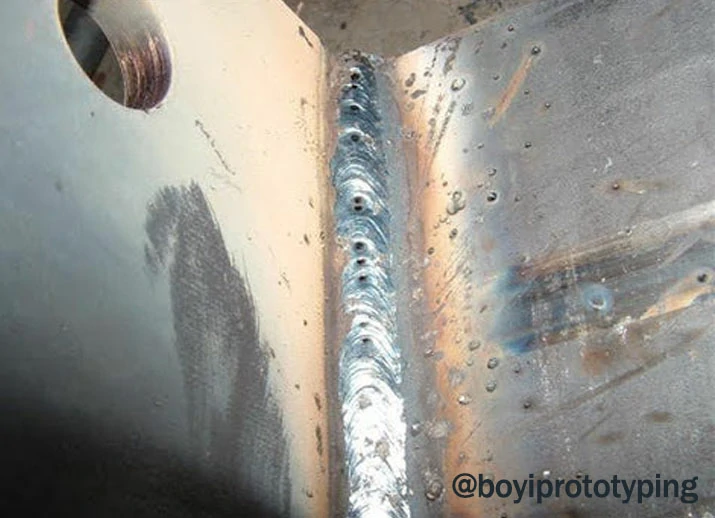
Elements Influencing Porosity Formation
The incident of porosity in welding is affected by a myriad of aspects, ranging from gas protecting efficiency to the intricacies of welding specification setups. Welding parameters, including voltage, current, take a trip rate, and electrode type, additionally effect porosity development. The welding method employed, such as gas metal arc welding (GMAW) or secured steel arc welding (SMAW), can influence porosity development due to variations in warm circulation and gas protection - What is Porosity.
Results of Porosity on Weld Quality
Porosity formation considerably jeopardizes the structural stability and mechanical buildings of welded joints. When porosity is present in a weld, it produces gaps or tooth cavities within the product, lowering the total stamina of the joint. These gaps work as stress and anxiety concentration points, making the weld much more prone to splitting and failure under tons. The visibility of porosity additionally weakens the weld's resistance to corrosion, as the trapped air or gases within the voids can react with the surrounding setting, leading to degradation over time. Additionally, porosity can hinder the weld's ability to withstand stress or influence, more threatening the total top quality and reliability of the bonded framework. In critical applications such as aerospace, automotive, or structural constructions, where security and sturdiness are look at more info paramount, the harmful results of porosity on weld quality can have extreme consequences, stressing the significance of minimizing porosity via correct welding methods and treatments.
Methods to Minimize Porosity
To boost the quality of bonded joints and ensure architectural stability, welders and makers utilize details methods aimed at minimizing the formation of voids and cavities within the product throughout the welding process. One reliable approach to decrease porosity is to make sure appropriate product preparation. This consists of extensive cleansing of the base steel to get rid of any type of impurities such as oil, grease, or wetness that might contribute to porosity development. Additionally, using the proper welding criteria, such as the appropriate voltage, existing, and take a trip speed, is vital in preventing porosity. Preserving a consistent arc length and angle throughout welding likewise aids lower the likelihood of porosity.

Moreover, choosing the appropriate securing gas and keeping proper gas flow rates are crucial in minimizing porosity. Using the suitable welding technique, such as back-stepping or employing a weaving motion, can likewise aid disperse warm equally and lower the opportunities of porosity formation. Making sure appropriate ventilation in the welding environment to get rid of any kind of prospective sources of contamination is crucial for accomplishing porosity-free welds. By executing these techniques, welders can effectively reduce porosity and produce high-quality bonded joints.
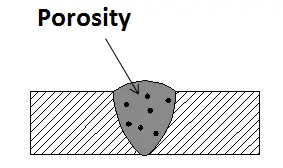
Advanced Solutions for Porosity Control
Carrying out innovative technologies and cutting-edge approaches plays a critical function in achieving premium control over porosity in welding processes. One advanced remedy is using sophisticated gas mixtures. Securing gases like helium or a combination of argon and hydrogen can help lower porosity by giving far better arc security and boosted gas coverage. Furthermore, using sophisticated welding techniques such as pulsed MIG welding or customized atmosphere welding can also aid minimize porosity concerns.
Another advanced solution entails making use of advanced welding tools. For instance, making use of equipment with integrated functions like waveform control and sophisticated source of power can improve weld high quality and decrease porosity risks. The execution of automated welding systems with precise control over criteria can substantially lessen porosity flaws.
Additionally, including innovative surveillance and assessment technologies such as real-time X-ray imaging or automated ultrasonic screening can assist in spotting porosity early in the welding process, enabling instant corrective actions. On the whole, integrating these innovative remedies can greatly our website improve porosity control and improve the total top quality of welded components.
Conclusion
In verdict, comprehending the science behind porosity in welding is necessary for welders and makers to generate high-grade welds - What is Porosity. Advanced solutions for porosity control can discover here better enhance the welding procedure and make certain a strong and reliable weld.
Comments on “How to Determine What is Porosity in Welding and Improve Your Strategy”